The Significance of Industrial Location Models in Modern Business
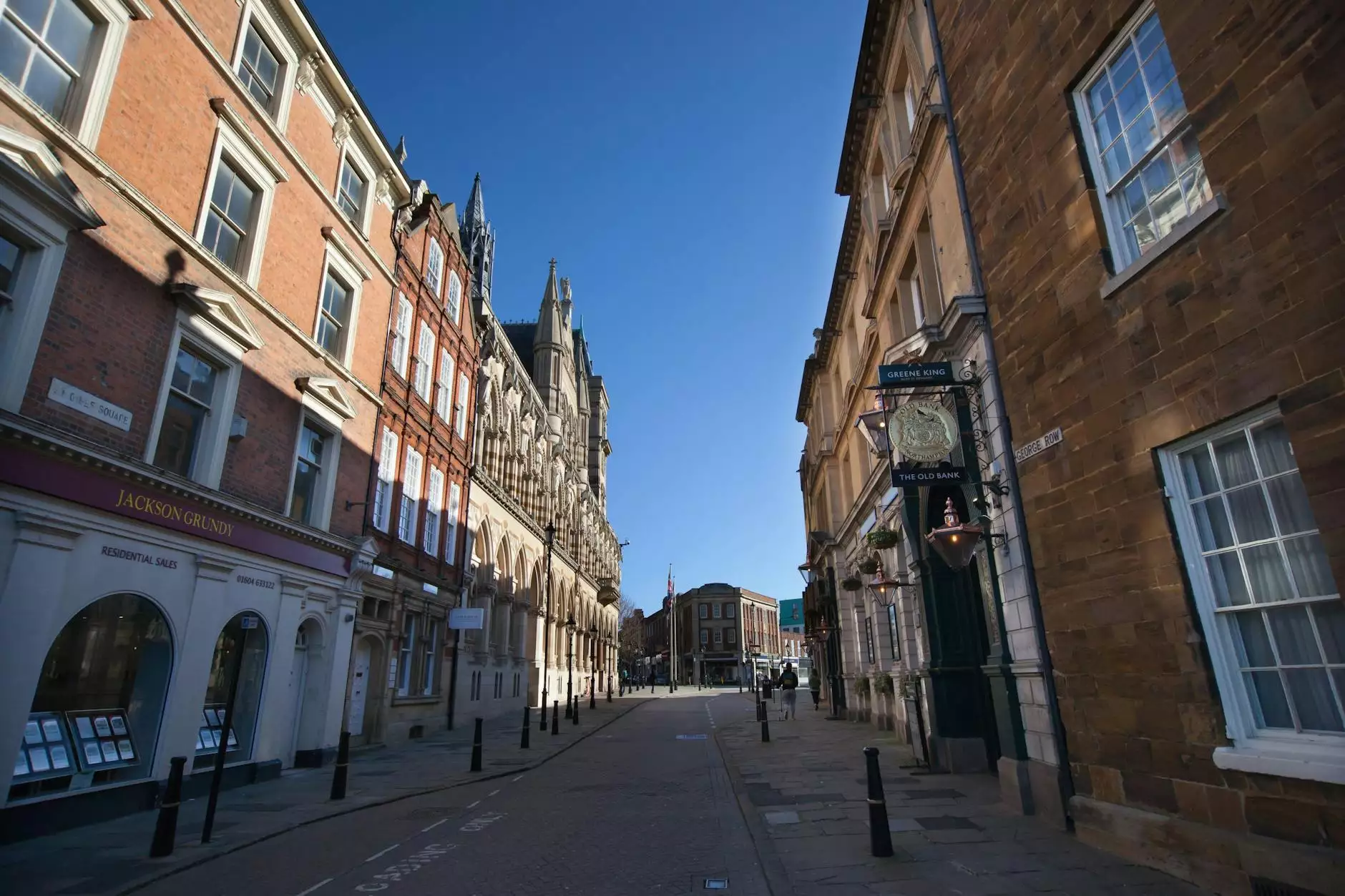
In today's competitive business landscape, understanding the significance of the industrial location model is crucial for companies seeking to optimize their operations and improve profitability. These models help in the strategic planning of business locations, ensuring that enterprises are positioned in a manner that maximizes their growth potential while minimizing costs.
What is an Industrial Location Model?
The industrial location model is a theoretical framework used to determine the optimal location for manufacturing and industrial activities. Established by economists and geographers, these models analyze various factors that influence the site selection process, including:
- Transportation costs
- Labor availability
- Raw material proximity
- Market accessibility
- Government policies
- Environmental considerations
The Importance of Choosing the Right Location
Choosing the right location for an industrial facility is more than just a logistical challenge; it's a strategic decision that affects the long-term viability of a business. Here are some compelling reasons why the industrial location model plays a pivotal role:
1. Cost Reduction
One of the primary objectives of the industrial location model is to minimize operational costs. By analyzing transportation routes and material supply chains, businesses can significantly reduce expenses on shipping and logistics. For instance, a company situated near essential suppliers can decrease delivery times and costs.
2. Access to Skilled Labor
Another critical factor in the industrial location model is the availability of skilled labor. Companies must analyze the local labor market to ensure they can recruit the necessary workforce. Areas with higher educational institutions and training facilities often yield a better talent pool, enhancing a company's competitive edge.
3. Enhancing Market Reach
The strategic placement of an industrial entity allows for better accessibility to key markets. Companies that utilize the industrial location model can identify locations that provide proximity to target demographics, thereby increasing market penetration.
4. Compliance with Regulations
Local, state, and federal regulations can vary significantly, impacting operational viability. The industrial location model aids businesses in finding locations that not only comply with laws but also offer incentives such as tax credits or subsidies.
Key Components of the Industrial Location Model
To effectively apply the industrial location model, businesses must consider several components:
A. Transportation Networks
Robust transportation networks are crucial for any industrial operation. The availability of highways, railroads, ports, and airports can greatly influence site selection. Efficient transportation reduces costs and time, enabling quick product distribution and resource acquisition.
B. Proximity to Suppliers
Being near suppliers can be beneficial for industries that rely on just-in-time inventory systems. The industrial location model emphasizes a thorough analysis of supply chains to ensure that raw materials and components are readily available, minimizing delays in production.
C. Market Accessibility
Understanding customer demographics and market dynamics is essential. The industrial location model encourages businesses to locate facilities where they can easily reach their customer base, whether through direct sales or distribution channels. This not only improves customer satisfaction but also drives sales growth.
D. Environmental Factors
More businesses are becoming conscious of their environmental footprint. The industrial location model considers environmental regulations and community impact, encouraging companies to choose locations that promote sustainable practices.
Applications of Industrial Location Models in Architecture
For architects, understanding the industrial location model can significantly enhance the design and strategic planning of industrial facilities. By integrating these principles into architectural planning, architects can:
- Design spaces that accommodate efficient workflows and operations.
- Ensure that buildings are situated to promote sustainability and collaboration.
- Create flexible spaces that can adapt to changing market demands.
Case Studies: Successful Implementation of Location Models
Numerous companies have successfully utilized the industrial location model to bolster their operations. Here are a few noteworthy examples:
1. Toyota's Production System
Toyota has long been a leader in the automotive industry, largely due to its effective application of the industrial location model. By positioning plants near suppliers and customers, Toyota minimizes waste and maximizes efficiency, embodying the principles of lean manufacturing.
2. Amazon's Fulfillment Centers
Amazon has strategically located its fulfillment centers across the globe, optimizing for rapid delivery times. The use of industrial location models enables Amazon to understand demographic trends and consumer behaviors, allowing for quick adjustments to their network as market demands shift.
Challenges in Applying Industrial Location Models
While the benefits of using the industrial location model are clear, challenges do exist:
A. Data Availability
Accurate and comprehensive data is essential for effective analysis. Without it, businesses may struggle to make informed decisions regarding location selection.
B. Changing Economic Conditions
Evolving economic conditions can impact the feasibility of a chosen location. Companies must remain agile and willing to revisit their location strategies in response to market changes.
Future Trends in Industrial Location Models
As technology and globalization continue to evolve, so too will the industrial location model. Here are some trends that are shaping the future:
1. Automation and Robotics
The rise of automation tools is altering traditional location planning. As industries embrace robotics for efficiency, the need for proximity to labor may diminish, allowing for new strategic site selections.
2. Emphasis on Sustainability
Increasing awareness of environmental issues is driving businesses to prioritize sustainable practices in their location strategies. The future application of the industrial location model will likely include comprehensive evaluations of environmental impacts.
3. Technological Integration
Advancements in data analytics and geographic information systems (GIS) will enhance the application of location models. Companies that leverage these technologies will gain insights that drive more informed decision-making and improve operational efficiencies.
Conclusion
The industrial location model remains an invaluable tool for businesses looking to optimize their operations and strategic planning. By considering transportation, labor, market access, and environmental impact, companies can successfully identify the most advantageous locations for their industrial activities.
As businesses evolve and new technologies emerge, continual refinement of these models will be necessary to maintain competitive advantage. For architects and planners, integrating these principles into design not only creates functional spaces but also enhances the long-term sustainability and profitability of industrial sites.
By understanding and utilizing the industrial location model, organizations can position themselves for success in an ever-changing marketplace.