Uncovering the Excellence of China CNC Lathe Machine Parts Manufacturers
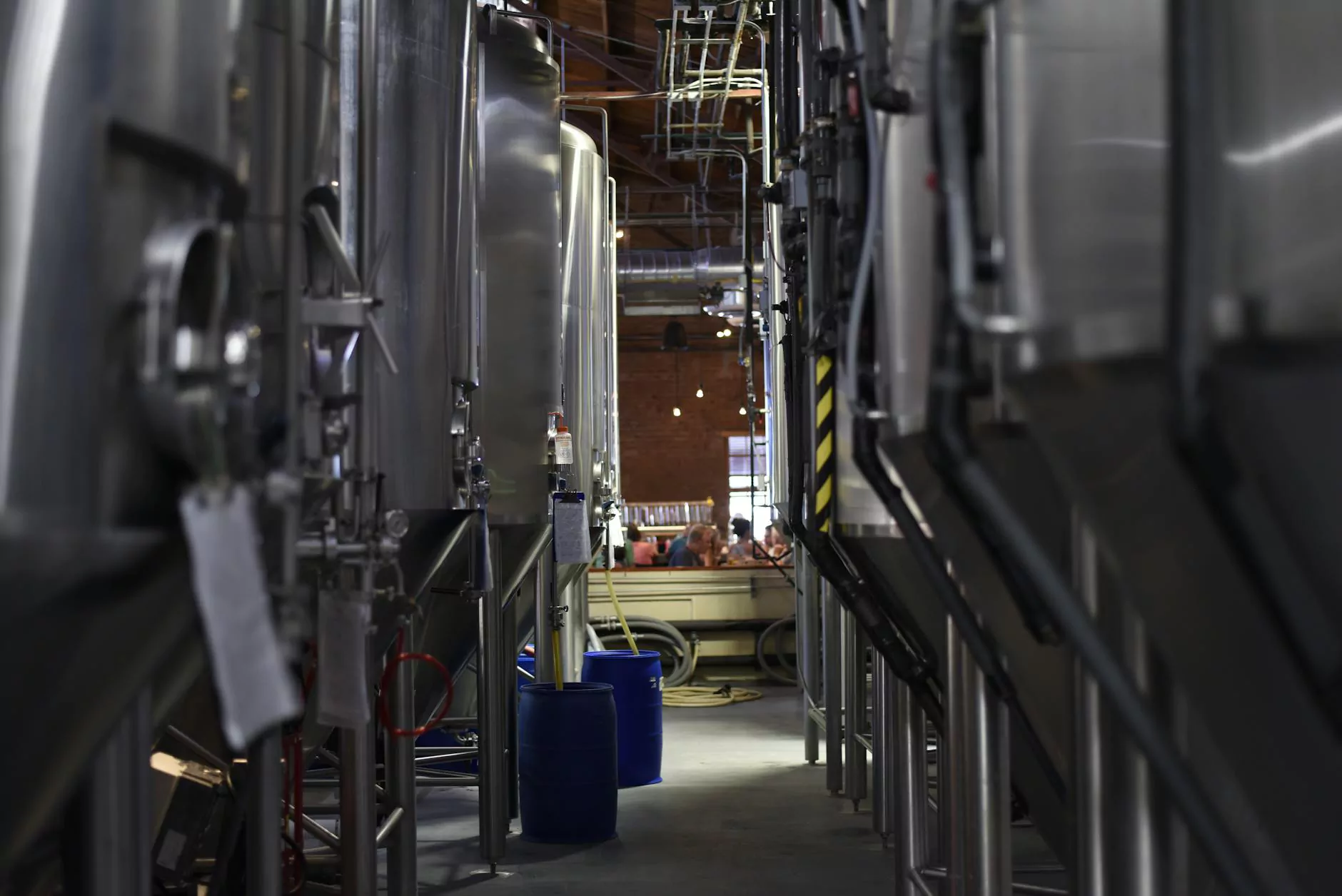
The Significance of CNC Lathe Machines in Modern Manufacturing
CNC (Computer Numerical Control) lathe machines are pivotal in the realm of precision manufacturing. They transform raw materials into intricate and highly accurate parts, making them indispensable for multiple industries, including aerospace, automotive, and medical. This technology embodies the pinnacle of efficiency and productivity, allowing manufacturers to create complex shapes and patterns with unparalleled precision.
Why Choose China CNC Lathe Machine Parts Manufacturers?
When it comes to securing the best CNC lathe machine parts, China stands out as a manufacturing titan. Here are some reasons why:
- Cost-Effectiveness: China is known for its competitive pricing structures due to lower manufacturing costs, making it a go-to destination for businesses seeking quality components without overspending.
- Skilled Workforce: The country boasts a vast pool of skilled technicians and engineers who specialize in CNC machining, ensuring that your products are made with expertise and proficiency.
- Advanced Technology: Many manufacturers in China utilize state-of-the-art machinery and software for CNC machining, resulting in superior products that meet international standards.
- Versatility: Chinese manufacturers have the capability to work with various materials such as metals, plastics, and composites, making them suitable for diverse applications.
- Rapid Production: High-efficiency processes and large-scale production capabilities ensure faster turnaround times for orders, enabling companies to meet tight deadlines.
The Major Players in the Chinese CNC Lathe Machine Parts Manufacturing Sector
Among the vast network of manufacturers in China, several companies have earned a stellar reputation for producing high-quality CNC lathe machine parts. These key players include:
- DeepMould: Known for its precision engineering and strict adherence to quality standards, DeepMould specializes in providing customized CNC lathe components that cater to their client's specifications.
- Shenzhen HXY Technology Co., Ltd: This manufacturer is recognized for its state-of-the-art CNC turning and milling services, producing parts that cater to industries like automotive and electronics.
- Dongguan Guohui Precision Machining: They focus on creating precision components that are extensively used in high-tech industries, combining experience with cutting-edge technology.
- Foshan Shunde Dingsheng Precision Machinery: With a specialization in high volume and precision CNC lathe machining, they cater to global markets and meet rigorous client requirements.
Understanding the Manufacturing Process
The journey of creating CNC lathe parts from conceptualization to final product involves several critical steps:
1. Design and Prototyping
The first step in manufacturing CNC lathe machine parts is design. Engineers utilize CAD (Computer-Aided Design) software to create detailed blueprints of the components. Prototyping may be conducted to ensure that the design meets functional requirements.
2. Material Selection
Once the designs are finalized, the next critical stage is choosing the right materials. Common materials for CNC machining include:
- Aluminum: Lightweight and corrosion-resistant, ideal for many applications.
- Stainless Steel: Offers outstanding durability and strength, suitable for medical and automotive components.
- Brass: Known for its excellent machinability and aesthetic appeal, often used in decorative parts.
- Plastics: Engineered plastics like Nylon and PTFE coat specific applications where metal isn't the ideal choice.
3. Machining Process
The actual machining begins with loading materials into the CNC lathe. The computer system guides the lathe to cut the material according to the specifications provided in the initial design. This process ensures precision and reduces the chance of human error.
4. Quality Control
Quality control is an essential aspect of manufacturing CNC lathe parts. After production, parts undergo rigorous testing and inspection to ensure they meet the desired specifications. This may include dimensional checks, surface finish assessments, and functional tests.
5. Delivery and After-Sales Support
Once parts pass inspection, they are packaged and shipped. Many manufacturers offer after-sales support, which can include assistance with installations or further modifications to enhance the final product's functionality.
Quality Standards in Chinese CNC Lathe Parts Manufacturing
The quality of CNC lathe parts produced in China is governed by various international standards. Key quality certifications include:
- ISO 9001: A quality management system standard that helps organizations ensure they meet customer and regulatory requirements.
- ISO/TS 16949: This standard focuses on quality management in the automotive industry, ensuring high levels of quality and consistency.
- RoHS Compliance: Electronics manufacturers must comply with this directive, which restricts hazardous substances in electrical and electronic equipment.
Challenges Faced by Chinese CNC Lathe Machine Parts Manufacturers
Despite the advantages, manufacturers in China face several challenges:
- Competition: The influx of manufacturers has led to intense competition, driving prices down but also impacting profit margins.
- Quality Control: Maintaining consistent quality across all products can be difficult, especially with varying levels of expertise among manufacturers.
- Supply Chain Issues: Global supply chain disruptions can affect material availability and overall production schedules.
- Technological Advancements: Keeping up with rapid technological changes requires substantial investment in training and new machinery.
The Future of CNC Lathe Machine Parts Manufacturing in China
The future for China CNC Lathe Machine Parts Manufacturers looks promising as technology continues to evolve. Industry trends indicate a shift towards:
- Smart Manufacturing: The integration of IoT (Internet of Things) to enhance productivity and efficiency.
- Automation: Increased automation will streamline processes, reduce labor costs, and minimize errors.
- Sustainability: Manufacturers are placed under pressure to adopt environmentally-friendly practices and reduce waste.
- Customization: The growing demand for customized products will drive manufacturers to be flexible and responsive to market changes.
Conclusion
In conclusion, China CNC lathe machine parts manufacturers embody a blend of expertise, advanced technology, and competitive pricing. Businesses looking for reliable, high-quality components will find strong allies in these manufacturers. By understanding the intricacies of the manufacturing process as well as the challenges faced, companies can make informed decisions that will drive their success in an increasingly competitive marketplace. Partnering with the right manufacturer, like DeepMould, can significantly enhance production capabilities and overall business efficiency.