Understanding Die Casting Tooling: Essential Insights for Metal Fabricators
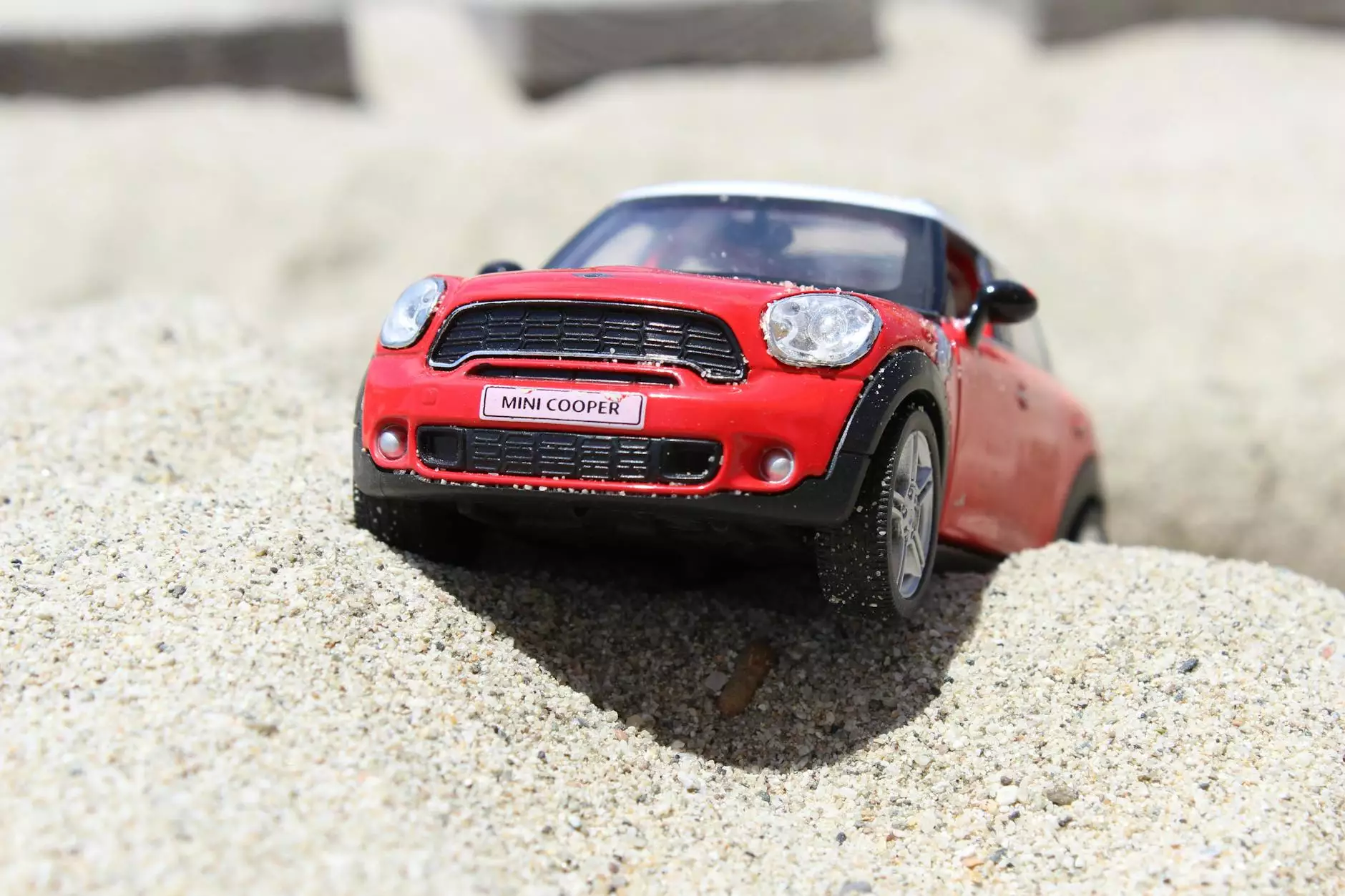
In the ever-evolving landscape of manufacturing, die casting tooling occupies a pivotal position, particularly for those in the sector of metal fabricators. This process not only enhances production efficiency but also enables the creation of highly detailed and precise components. In this article, we will delve deep into the intricacies of die casting tooling, examining its benefits, processes, and best practices in the industry.
What is Die Casting Tooling?
Die casting tooling refers to the specialized molds and components used in the die casting process. Die casting itself is a method that involves forcing molten metal into a mold under high pressure. This technique is widely employed to produce complex shapes with excellent dimensional accuracy, allowing metal fabricators to meet stringent specifications.
The Benefits of Die Casting Tooling
The advantages of utilizing die casting tooling are numerous and impactful. Below are some of the most significant benefits:
- High Precision and Repeatability: Die casting allows for the production of parts that are consistent in size and shape, crucial for industries that demand precision.
- Material Efficiency: Minimal waste is generated in the die casting process, which translates to reduced material costs and a smaller environmental footprint.
- Strength and Durability: Components produced through die casting often exhibit superior strength, making them ideal for demanding applications.
- Complex Geometries: The versatility of die casting tooling supports the creation of intricate designs that may be challenging or impossible with other manufacturing methods.
- Cost-Effective Production: For high-volume production runs, die casting tooling can lead to significant cost savings, as the per-unit cost decreases with increased output.
The Die Casting Process Explained
Understanding the die casting process is critical for maximizing the use of die casting tooling. The process generally follows these steps:
- Mold Design: Creating an efficient mold design that can withstand high temperatures and pressures is crucial.
- Melting the Metal: The metal is melted in a furnace and prepared for casting.
- Inserting the Mold: The molten metal is injected into the mold at high pressure, ensuring it fills all cavities.
- Cooling: The metal cools and solidifies within the mold.
- Mold Removal: The mold is opened, and the cast part is ejected.
- Finishing: Any additional finishing processes, such as trimming or surface treatment, are applied to achieve the desired specifications.
Choosing the Right Die Casting Tooling Materials
The performance of die casting tooling is significantly affected by the materials used. Here are some common materials employed in die casting tooling:
- Aluminum Alloys: Known for their light weight and strength, aluminum alloys are frequently used, especially in automotive applications.
- Zinc Alloys: These alloys offer excellent fluidity and are often employed for smaller, intricate parts.
- Magnesium Alloys: As the lightest structural metal, magnesium is used where weight reduction is essential.
- Steel: Durable and long-lasting, steel is used for tooling that must withstand extensive use and high temperatures.
Best Practices for Die Casting Tooling
To ensure optimal performance and longevity of die casting tooling, manufacturers should adhere to several best practices:
- Regular Maintenance: Implement a routine maintenance schedule to inspect the tooling for wear and tear.
- Temperature Control: Maintain consistent temperatures during both the melting and cooling phases to prevent defects.
- Quality Materials: Invest in high-quality materials for both the tooling and the casted components to enhance durability.
- Design Optimization: Optimize mold designs considering the characteristics of the metal being used.
- Training and Expertise: Employ skilled technicians familiar with die casting tooling processes to ensure best practices are followed.
Future Trends in Die Casting Tooling
The landscape of die casting tooling is continuously evolving due to advancements in technology and changing industry needs. Here are some emerging trends to watch:
- Automation and Robotics: The integration of robotics into the die casting process can enhance precision and production speed.
- 3D Printing of Tooling: The use of additive manufacturing to create tooling components is gaining traction, allowing for more complex designs and reduced lead times.
- Sustainable Practices: Increasingly, companies are looking for ways to make their die casting processes more sustainable, utilizing recyclable materials and minimizing waste.
Conclusion: Elevating Your Metal Fabrication with Die Casting Tooling
In conclusion, die casting tooling is an essential element of the metal fabrication industry, playing a crucial role in producing high-quality components with precision and efficiency. By understanding the process, choosing the right materials, and adhering to best practices, metal fabricators can significantly enhance their production capabilities. As technology continues to advance, staying informed about trends and innovations in die casting tooling will be vital for maintaining a competitive edge.
For more insights and support in metal fabrication, explore our services at deepmould.net and discover how we can assist you in mastering die casting tooling.