CNC Precision Machining Parts Factory: Elevating Manufacturing Excellence
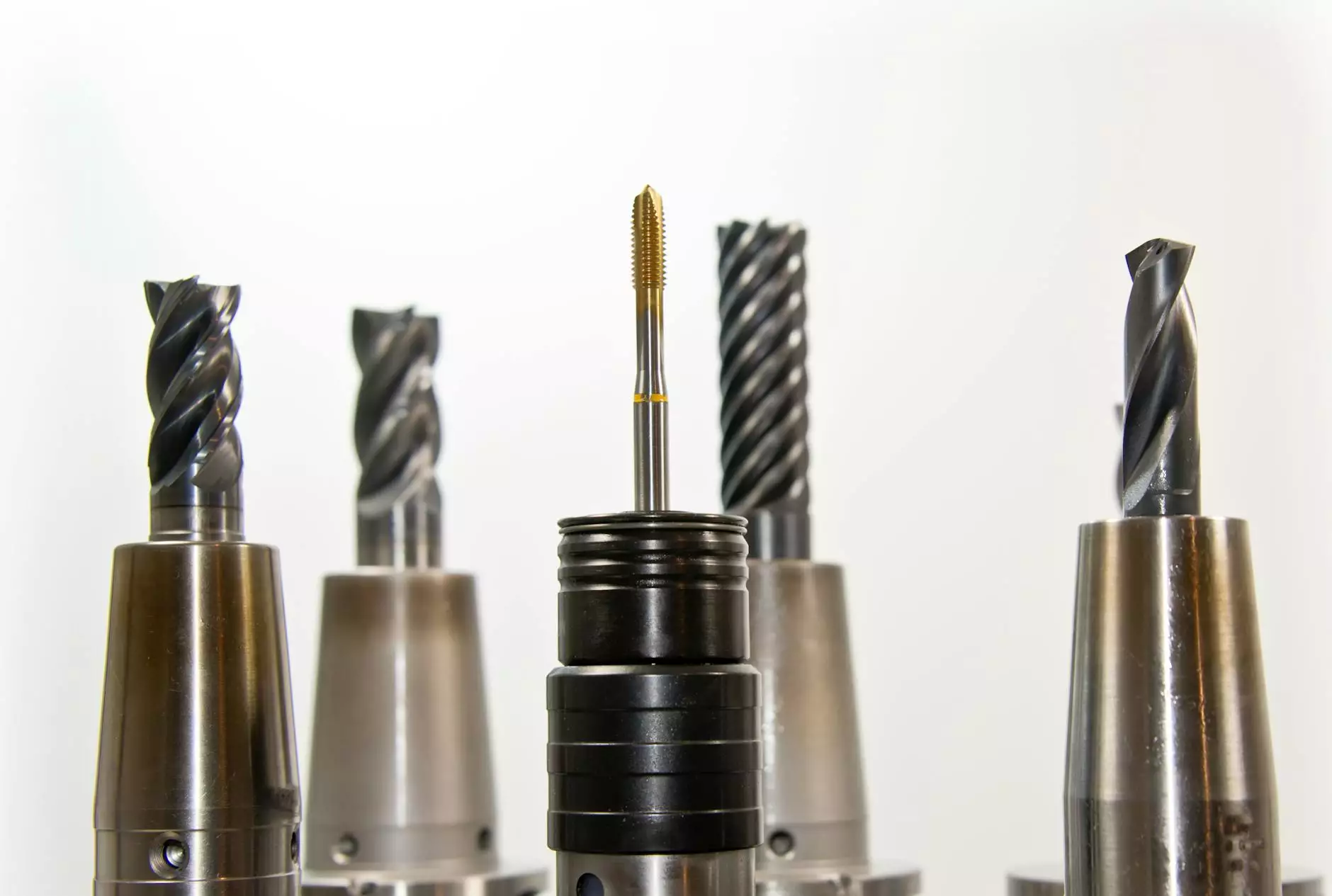
The landscape of manufacturing today is rapidly evolving, and at the heart of this evolution lies the cnc precision machining parts factory. These facilities are the backbone of modern production, leveraging advanced technology and skilled craftsmanship to create components with unparalleled precision. As businesses strive for excellence, understanding the role of CNC machining becomes paramount. This article delves into the intricacies of CNC precision machining, its advantages, processes, and the future of manufacturing.
The Foundation of CNC Precision Machining
CNC, or Computer Numerical Control, refers to the automated control of machining tools by means of a computer. This technology has transformed traditional machining processes, allowing for a level of precision and consistency that was previously unattainable.
In a typical cnc precision machining parts factory, various processes work in harmony to produce high-quality metal components. The main types of CNC machining include:
- Milling: A process where rotating tools remove material from a workpiece, creating various shapes and features.
- Turning: This involves rotating the workpiece while a cutting tool shapes it, commonly used for cylindrical parts.
- Drilling: Creating holes in materials using a rotating drill bit.
- EDM (Electrical Discharge Machining): Uses electrical discharges to remove material, ideal for intricate designs.
Key Advantages of CNC Precision Machining
Utilizing CNC machining offers numerous advantages that set it apart from traditional manufacturing methods. Here are some key benefits:
1. Enhanced Precision and Accuracy
One of the most significant advantages of CNC machining is its ability to achieve exceptional precision. The integration of computer controls allows for minimal human error, ensuring that each component is manufactured to exact specifications.
2. Improved Efficiency
CNC machines operate continuously, significantly reducing the time required to manufacture parts. Automated processes lead to faster production cycles, which in turn increases overall efficiency.
3. Flexibility in Design
The capability to create complex geometries and custom designs makes CNC machining a versatile option for manufacturers. Clients can modify designs easily as changing a program is more efficient than altering physical setups.
4. Cost-Effectiveness
While the initial investment in CNC technology can be high, the long-term savings achieved through reduced labor costs, fewer errors, and higher productivity make it a cost-effective solution for many businesses.
5. Consistency in Production
Once a design is programmed into the CNC machine, each piece produced will be virtually identical, ensuring that quality remains constant across large production runs.
Process Overview in a CNC Precision Machining Parts Factory
The operational workflow in a cnc precision machining parts factory involves several critical steps:
Step 1: Design and Engineering
The process begins with design and engineering. Skilled engineers create detailed CAD (Computer-Aided Design) models of the required parts. These models serve as the blueprint for the CNC machine, defining shapes, dimensions, and tolerances.
Step 2: Programming
Once the CAD model is complete, the next step is programming. CNC programmers translate the CAD designs into CNC code using CAM (Computer-Aided Manufacturing) software. This code contains precise commands that dictate the movements of the machine.
Step 3: Material Selection
Choosing the right material is critical for achieving the desired properties in the finished product. Common materials used in CNC machining include:
- Aluminum
- Steel
- Brass
- Plastic (e.g., acrylic, nylon)
Step 4: Machining Process
The machining process involves setting up the CNC machine, securing the workpiece, and executing the code. This step is where the physical transformation occurs as the machine removes material to create the desired part.
Step 5: Quality Control
Quality control is a crucial part of the manufacturing process. After machining, each part undergoes rigorous inspection using various tools and techniques to ensure it meets the required specifications. This is vital for maintaining high standards and satisfying customer expectations.
Applications of CNC Precision Machined Parts
CNC precision machined parts find applications in numerous industries. Here are some key areas where these components play a fundamental role:
Aerospace Industry
The aerospace industry demands the highest level of precision and reliability. Components such as engine parts, landing gear, and structural elements are frequently produced using CNC machining technology.
Automotive Sector
In the automotive sector, CNC machined parts are used for everything from engine components to transmission parts. The emphasis on performance and safety necessitates the use of precision engineering.
Medical Equipment
The medical field relies on CNC machining for producing complex surgical instruments, prosthetics, and implants. Each piece must meet stringent regulatory standards for quality and precision.
Electronics
CNC machining is essential in the production of housings, brackets, and components for electronic devices. As devices become smaller and more intricate, precision becomes increasingly important.
The Future of CNC Precision Machining
As technology progresses, the future of CNC precision machining looks promising. We are witnessing advancements in several areas:
1. Integration of Automation
The incorporation of automation into CNC machining processes is enhancing efficiency. Automated loading and unloading systems, along with robotic arms, enable factories to operate with minimal human intervention.
2. Increased Use of AI and Machine Learning
Artificial intelligence is being integrated into CNC machining systems, helping to optimize manufacturing processes. Machine learning algorithms can analyze performance data to improve production methods continuously.
3. Sustainability and Eco-Friendly Practices
As industries move towards sustainability, CNC machining is adapting by implementing measures to reduce waste and energy consumption. Recycling materials and utilizing energy-efficient machines are becoming standard practices.
4. Advancements in Materials
New materials are being developed that offer superior strength, lightweight properties, and corrosion resistance. The ability to machine these materials expands the potential applications for CNC technology further.
Conclusion: The Impact of CNC Precision Machining on Modern Manufacturing
In conclusion, the role of the cnc precision machining parts factory in the manufacturing industry cannot be overstated. As we continue to embrace technology, the benefits of CNC machining will only grow, creating endless possibilities for businesses across various sectors. By understanding the processes, advantages, and future trends of CNC machining, manufacturers can harness this powerful technology to improve efficiency, quality, and innovation in their production lines.
For more information on precision machining and how it can benefit your business, visit deepmould.net.